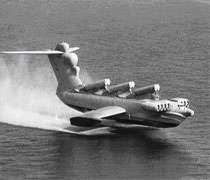
ماشین WIG یک نوع پرنده است که در ارتفاع حدودا ً ده پایی (سه تا چهار متر) پرواز می کند. در چنین ارتفاعی WIG از یک اصل ویژه ی آیرودینامیکی به نام اثر زمین بهره می گیرد. حال برای تشریح اثر زمین و چگونگی شکل گیری آن نیاز به یادآوری چند خصوصیت آیرودینامیکی بال هواپیما می باشد.
همان طور که می دانیم بال یک هواپیما lift تولید می کند و این نیرو از اختلاف فشار موجود در بال حاصل می گردد به طوری که فشار در زیر بال بیشتر از فشار بر روی بال می باشد. امّا از آنجایی که جهان همواره به سوی تعادل در حرکت است، جریان پر فشار زیر بال میل به جاری شدن به منطقه ی کم فشار (بالای بال) دارد که این جریان فقط از نوک بال مقدور می باشد. اثر حاصل از این جریان، جریانات حلقوی نوک بال می باشد و از آنجایی که در حین پرواز بال به سمت جلو در حرکت می باشد، این جریانات حلقوی در هوا به دنبال بال کشیده می شوند، به همین دلیل به این جریانات trailing vortex گفته می شود. جریان حلقوی نوک بال چپ در خلاف جهت جریان حلقوی نوک بال راست می گردد.
تشکیل trailing vortex به علت اختلاف فشار در بالا و پائین بال
مهمترین اثر جریانات حلقوی منحرف کردن جریان هوای پشت بال به سمت پائین می باشد. جزئی از بردار سرعت را که در اثر جریانات حلقوی به پائین منحرف شده downwash می گویند، که باعث کاهش lift می گردد. برای جبران lift از دست رفته باید زاویه ی حمله ی بال افزایش یابد که همین افزایش زاویه ی حمله منجر به افزایش induced drag می شود.
کاهش lift و افزایش drag در اثر downwash
حال ببینیم هنگامی که یک هواپیما در نزدیکی زمین پرواز می کند چه روی می دهد؟
این اثر بیشتر به وسیله ی خلبانان در هنگام فرود مشاهده می شد. آنان، هنگام فرود احساس معلق بودن و یا سوار بودن بر بالشتکی از هوا می کردند. این اثر چیزی نبود، جز افزایش ناگهانی lift در نزدیکی زمین که منجر به دشوار شدن عمل فرود می شد. در نزدیکی زمین trailing vortex ها به وسیله ی زمین نگه داشته می شوند . این عمل باعث کاهش downwash می شود که نهایتا ً منجر به افزایش lift می گردد و اصطلاحا ً زاویه ی حمله ی موثر افزایش یافته است، و این همان اثر زمین می باشد.
شکل گیری کامل trailing vortex ها در ارتفات:
متراکم شدن trailing vortex ها در نزدیکی زمین:
گیر کردن و مسدود شدن trailing vortex ها به وسیله ی زمین:
Lift اضافه شده حاصل از اثر زمین را ram pressure گویند. هر چه فاصله ی مابین، بال و زمین کاهش یابد اثر این پدیده افزایش می یابد چرا که با کاهش این فاصله هوای جاری در این بین بیشتر فشرده می شود بنابراین فشار هوای زیر بال افزایش می یابد که نهایتا ً منجر به افزایش lift می گردد.
باید در نظر داشت که اگر میزان فاصله ی بال و زمین از فاصله ی بین دو نوک بال بیشتر شود اثر زمین وجود نخواهد داشت.
در ارتفاعی به میزان 1/10 ام wingspan میزان induced drag به نصف کاهش می یابد.
نمودار زیر نقش ارتفاع را روشن می سازد.
نمودار کاهش includ drag به علت زمین
بنابر مطالب یاد شده، ماشین پرنده ای که در حین پرواز از اثر زمین استفاده نماید، بسیار بهینه تر از حالتی خواهد بود که در ارتفاعات پرواز کند. همچنین باید دانست که این بهینه شدن حاصل از بزرگ شدن L/D می باشد.
در حال حاضر L/D مربوط به هواپیماهای زیر سرعت صوت بین 15 تا 20 می باشد، حال آنکه این عدد برای یک WIG بین 25 تا 30 می باشد.
در آینده می توان از WIG به عنوان تاکسی آبی بهره جست. این پرنده ها حتی می توانند در آبهایی که ارتفاع موج آن ها به دو متر می رسد، در حرکت باشند.
یک WIG در مکان های زیر می تواند به خوبی کاربرد داشته باشد.
• دریاهای نسبتا ً آرام مانند بالتیک و مدیترانه
• دریاچه های بزرگ
• رودخانه های دلتایی بزرگ
• مناطق ساحلی
• مجمع الجزایرها (مانند مجمع الجزایر جنوب شرقی آسیا)
با ساخت WIG های بزرگ می توان کاربرد آن ها را گسترش داد، به عنوان مثال یک نوع از این پرنده با نام AR-1 Atlantis توانایی حمل بار تا پنج تن را داراست.
AR-1 Atlantis
در مورد رده بندی WIG ها باید گفت که این پرنده ها به چهار رده تقسیم می شوند و این رده بندی بنابر عملکرد آنها صورت پذیرفته.
1. کلاس HSC: این نوع در تمام مدت با آب در تماس بوده و در اصل اثر زمین به عنوان یک عامل کمکی به کار گرفته شده است.
2. کلاس A: این نوع بدون اثر زمین قادر به فعالیّت نیست.
3. کلاس B: این نوع توانایی افزایش ارتفاع حتی تا خارج از حوزه ی اثر زمین را داراست.
4. کلاس C: این نوع WIG می تواند ارتفاع خود را به خوبی افزایش دهد و حتی از طرف ICAO به عنوان یک هواپیما (با ارتفاع کم) دارای گواهینامه می باشد.
ناگفته نماند که اثر زمین در زمینه های دیگری نیز به کار گرفته می شود، به عنوان مثال در طراحی قایق های تندرو برای تعادل هرچه بیشتر این پدیده در نظر گرفته می شود.
در پایان تصویر و نام چند WIG قرار داده شده.
Lun Ekranoplan
Boeing Pelican
Flarecraft L-325
|