روش آلیاژسازی مکانیکی اولین بار توسط بنیامین(Benjamin) و همکاراناش در اواخر دهه شصت ِ قرن بیستم میلادی معرفی شد. آنها این روش را به منظور تولید سوپرآلیاژهای پایه نیکلی استحکام یافته با ذرات اکسیدی به کار بردند.
طی این فرایند، ذرات پودری خام در اندازه چند میکرون تحت یک تغییر شکل پلاستیکی شدید قرار میگیرند و پیوسته متحمل جوش سرد و شکست میشوند. چنانچه پودر مورد استفاده از نظر ترکیب شیمیایی کاملاً همگن باشد (برای مثال پودر یک عنصر یا پودر یک آلیاژ) فرایند، آسیاب کردن مکانیکی (( Mechanical Milling (MM)نامیده میشود. در این حالت، هیچگونه تغییری در ترکیب شیمیایی پودر اولیه صورت نمیگیرد و آلیاژسازی مکانیکی تنها منجر به تغییر در ساختار داخلی و اندازه ذرات پودر میگردد. سابقه تاریخی روش آسیاب کردن مکانیکی به سال 1987 برمیگردد. مزیت آن نسبت به دیگر روشها، اجرای آسان و کمهزینه در مقیاس صنعتی است.
فرایند تولید پودر و پارامترهای اصلی فرایند
ابتدا مواد خام را به همراه گلوله و مواد کنترل فرایند(PCA یا Process Control Agent) ، در داخل محفظه آسیاب میریزند. در اثر چرخش محفظهی آسیاب، گلولهها به مواد خام برخورد کرده، منجر به آسیاب شدن و خردتر شدن میشوند. در این بین نیز مواد خام به دلیل گیرافتادن بین گلولهها بر اثر جوش سرد، پرس و به هم متصل میشوند و ذرات بزرگتری به وجود میآورند. شکل 1 به زیبایی نحوه پروسه را توضیح میدهد.
در اولین مراحل آلیاژسازی مکانیکی به دلیل نرم بودن ذرات پودر، مکانیزم غالب، جوش سرد میباشد و در نتیجه اندازه ذرات پودر افزایش مییابد که این افزایش تا چند برابر اندازه اولیه ذرات پودر گزارش شده است. با ادامه تغییر شکل و کار سخت شدن ذرات پودر، تمایل به شکست در ذرات پودر افزایش مییابد. در نتیجه در مرحله دوم آلیاژسازی مکانیکی، اندازه ذرات پودر کاهش مییابد. در مرحله سوم و پس از گذشت زمان معینی حالت پایا بین سرعت جوش سرد و شکست به وجود میآید. در این شرایط اندازه ذرات ثابت میماند و تغییر نمیکند.
آسیابهای ستارهای (متداولترین نوع و محصول کارخانه Fritsh آلمان است)، شافتی(Attrition milling)، ارتعاشی( Shaker ball mill)، غلتشی( Tumbler mill )و مغناطیسی از متداولترین آسیابها هستند( شکل 2).
آسیابهای سیارهای یکی از انواع آسیابهای متداول در آلیاژسازی مکانیکی هستند که تا چند صد گرم پودر را در هر بار آسیاب میکنند. این نوع آسیاب شامل دو تا چهار محفظه است که روی یک دیسک نصب شدهاند. محفظهها حول محور عمودی خود دوران میکنند و به طور همزمان دیسک نگهدارنده محفظهها نیز در جهت مخالف با چرخش محفظهها دوران دارد. به این ترتیب، مطابق شکل (2-الف) محفظه دو نوع حرکت چرخشی خواهد داشت که در نتیجه گلولههای داخل محفظه آسیاب تا مسافتی به جداره داخلی آن چسبیده و در نقطهای معین از جداره جدا شده و به سمت مقابل برخورد میکنند.
در آسیاب ارتعاشی چند گلوله داخل محفظهای کوچک جای میگیرند و محفظه آسیاب که بر روی یک بازو محکم شده است با فرکانس بالا ارتعاش میکند (شکل 2-ب). در این آسیاب حرکات ارتعاشی در سه بعد صورت میگیرد به طوریکه دامنه حرکت در یک بعد بیشتر از دو بعد دیگر است. اگرچه سرعت خطی گلولهها در آسیاب گلولهای سیارهای بیشتر از آسیاب ارتعاشی است اما به دلیل فرکانس بالای ضربات در آسیاب ارتعاشی، این آسیاب نسبت به آسیاب ستارهای، پرانرژیتر محسوب میشود.
آسیابهای غلتشی از یک محفظه استوانهای بزرگ حاوی تعداد زیادی گلوله و یا میله تشکیل شده و ظرفیت بالایی در حدود 100-0.5 کیلوگرم دارا میباشند. محفظه به صورت افقی به وسیله دو غلتک چرخان میغلتد (شکل 2-ج). در این نوع آسیاب، گلولهها بر اثر نیروی گریز از مرکز تا مسافتی به دیواره محفظه چسبیده و بالا میروند. سپس با غلبه نیروی جاذبه در ارتفاع مشخصی به پایین سقوط میکنند. با تغییر سرعت چرخش غلتکها، سرعت آسیاب کرد نیز افزایش مییابد. اما بیش از یک سرعت بحرانی، نیروی گریز از مرکز بر جاذبه غلبه کرده و گلولهها به جداره استوانه میچسبند.
آسیابهای شافتی همانند آسیابهای غلتشی دارای یک محفظه استوانهای و تعداد زیادی گلوله بوده و ظرفیت تولید بالایی نیز دارند. در این نوع آسیابها، محفظه استوانهای ثابت است و حرکت گلولهها توسط تعدادی پروانه که بر روی یک شافت عمودی نصب شدهاند، صورت میگیرد (شکل 2-د). بنابراین، کنترل درجه حرارت به وسیله عبور یک سیال در فاصله بین دو جداره محفظه به سهولت فراهم میگردد. اما آببندی این گونه آسیابها برای انجام عملیات آلیاژسازی مکانیکی تحت شرایط خلأ یا اتمسفر خنثی مشکل است.
آسیاب مغناطیسی، عملکردی مشابه با آسیاب غلتشی دارد با این تفاوت که در این نوع آسیاب یک میدان مغناطیسی جایگزین نیروی جاذبه شده است (شکل 2-ه). این نوع آسیاب برای کاربردهای آزمایشگاهی مفید بوده و تا 100 گرم پودر را در هر مرحله آسیاب میکند.
آسیابهای غلتشی و شافتی نسبت به سایر آسیابها از انرژی کمتری برخوردار هستند اما به دلیل طرفیت بالای تولید، در مقیاس صنعتی قابل استفاده میباشند.
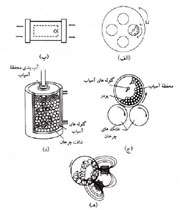
مواد کنترلی (PCA)<\/h2>
از آسیاب بدون PCA با توجه به جوش سرد نمیتوان انتظارنانوپودر داشت. که شدت جوش سرد مواد داکتیل زیاد است، به طوری که در یک آسیاب گلولهای معمولی، کمتر از 1% کاهش قطر پودر داریم و در آسیابهای گلولهای ویژه، این مقدار به یک درصد نمیرسد. برای حل این مشکل از PCA استفاده میکنیم. پس این مواد، مهمترین عامل در رسیدن به نانوپودر هستند. اغلب آنها موادی آلیاند که جذب سطح شده، از آگلومره شدن (کلوخهای شدن) آنها جلوگیری مینماید.
محدودهی ترکیبی این مواد وسیع است (میتوان از مواد مختلفی استفاده کرد). از مهمترین آنها میتوان هگزان، اسید استریک (نوعی اسید آلی)، متانول و اتانول را نام برد. تحقیقات نشان داده است که میزان حضور PCAها منجر به کاهش نمایی اندازهی ذرات میشوند. به عنوان مثال وقتی 1% وزنی اسید استریک به آلومینا اصافه کنیم، بعد از 5 ساعت اندازه ذرات 500 میکرومتر ولی اگر 3% اضافه کنیم در همین مدت به ذراتی با اندازهی 10 میکرومتر خواهیم رسید.
همچنین این مواد بر روی فاز نهایی، میزان حلالیت جامد و تغییرات میزان و نوع ناخالصی مؤثرند. البته بعضی مواقع محصولات جانبی واکنشهای آسیاب خود به عنوان PCA عمل میکنند؛ این حالت از نظر کنترل فرایند و آلوده نکردن محصول، بهترین حالت است. به عنوان مثال، در تولید زیرکونیا، کلرید زیرکونیوم را با منیزیا وارد آسیاب کرده، که در نتیجه داریم:
ZrCl4 + 2MgO = ZrO2 + 2MgCl2
محصول جانبی واکنش (کلرید منیزیم) به عنوان یک PCA عمل میکند و از به هم چسبیدن ذرات منفرد و نانوکریستال زیرکونیا ممانعت به عمل میآورد، و در پایان به راحتی با یک شستشو از محصول جدا میشود
|